Canada-based Engineer Ezenta Explains How Nigeria’s System Supports Building Crash
In this exclusive interview with Prime Business Africa, Canada-based structural engineer, Ben Ezenta, takes a look at the issues leading to the collapse of 21-storey building in Ikoyi as well as the recurring cases of building collapse in Lagos-Nigeria and the rest of the country. Engineer Ezenta speaks with Prime Business Africa’s VICTOR EZEJA on what the authorities must do to provide sustainable solutions to the menace.
How would you react to the recurring cases of building collapse in Nigeria, especially the controversial 21-storey disaster in Ikoyi?
We’re not getting a lot of things right. First of all, accidents don’t just happen. They are caused. Secondly, People don’t do what is expected, they do what is inspected. Finally, our system is not designed to avert building collapse; rather, they are designed to encourage building collapse. These may be provocative statements, but they are true. I’ve been working in the building industry in Calgary, Canada for over 17 years. There has been no incidence of a single case of building collapse throughout this period. It means that there are a lot of things they are doing right. There are a lot of high-rise and complex buildings in Calgary. They do not collapse, because things are done right. It might interest you to know that even here in Canada, people don’t voluntarily do what is expected. The system forces them to do the right thing. In contrast, our system forces people to do the wrong thing even when they intend to do the right thing.
Join our WhatsApp ChannelAs an international expert in Structures, could you explain the processes in other climes, which Nigeria has failed to imbibe?
I do not only have professional experience abroad, I have practical experience building in Nigeria. So, I can confidently speak from both professional experience abroad and practical experience in Nigeria. A little story: In 2012, I started some building projects in Lagos. I did the design as if I were building it here and followed all the building codes and city requirements in obtaining a building permit as if I’m going to build it here. When I got to Lagos, I went to the local government three times on three different days to obtain a building permit (something that would normally take an hour or two here in Canada). After sweating for those days at the local government office without any luck, some people advised me to go start my project and they would come to the site. True to fact, a couple of days later when we were excavating the foundations, they came. I was pleased to see them. Though the method (if it is truly how they operate) was somewhat odd or strange, as I was expecting them to review my drawings, make comments, stamp the drawings and tell me what to pay and issue me a building permit. Rather, they brought out the receipt and asked me to pay. I paid and was issued a receipt. To my greatest surprise, nobody asked to see my drawings, and nobody came to inspect the foundation. There and then I understood why buildings collapse in Nigeria.
Again, in 2020, I designed and was to build a warehouse in Owerri. The same thing happened, the difference this time is that the fee in Owerri was about 10 times the fees in Lagos. Yes, we submitted our building plans and paid all the necessary fees. However, nobody told me if my plans were correct, and they complied with the Nigerian building code. Secondly, nobody came to site to inspect any aspect of the project until the warehouse was completed.
That cannot happen in Canada. Even building a simple wooden deck more than 2 feet from grade, requires an engineer to design and stamp the drawing. Building permit process is very complex that I can write pages about it. A summary of the process will include the following:
First thing is for you to hire a designer or architect to design the building. The size and complexity of the building will determine if a professional, like an architect, will be involved.
Second is that you hire a structural engineer to design the structural parts of the building – foundation, beams, columns, floor system, roof and other load-bearing members. All the designs are guided by the building codes and standards.
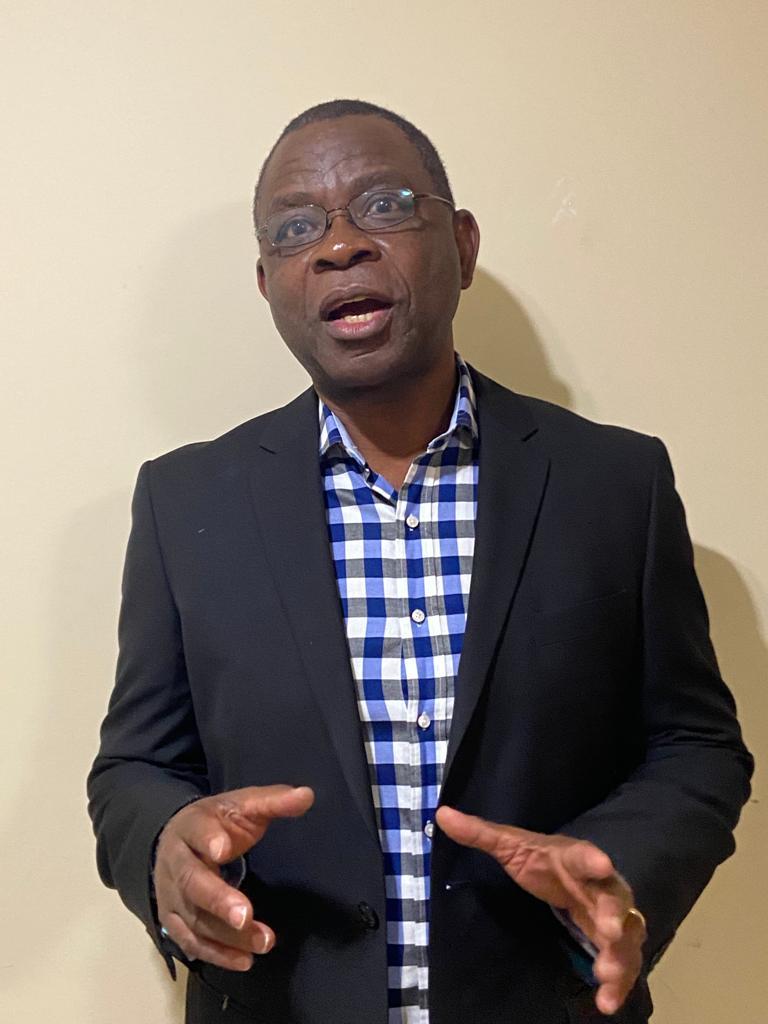
Three, you hire a geotechnical engineer to provide a bearing capacity of the soil as well the soil test to determine the presence, or otherwise, of sulphate in the soil. If sulphate is present, you must use sulphate resistant cement and not General Use (GU) cement.
If it is a commercial, industrial, high-rise or residential building over a certain size, a mechanical, electrical and civil engineer will be involved in addition to the architect and structural engineer.
Next is that you package all these and other documents and apply for a building permit. The city Safety Codes Offices will review the drawings for compliance with building, electrical, plumbing and mechanical codes. The design engineer takes responsibilities and liabilities for their design. The city defers to engineers where an engineer is involved except were the design not compliant with the building code.
Again, if all the conditions are met, the city issues you a building permit with conditions of what you must do in the process as well as documents to be submitted in the cause of the building process. The most important aspect of the permit conditions is the milestones during which you must call the city for inspection. These are:
i. Foundation stage for rebar (reinforcement) prior to placement of concrete
ii. Inspection of the concrete foundation prior to backfill
iii. Rebar cage for columns, slabs, beams etc.
iv. You must submit a concrete delivering slip to the structural engineer to ascertain if the concrete used is in accordance with the design. Also, the slump, cube crushing tests at 7, 14 and 28 days are submitted to the engineer.
v. Other inspections will include electrical, plumbing, gas, and mechanical rough-ins and final inspections
vi. The engineer is required to complete different Schedules for design, field review as well as total compliance to codes and standards. I’ve summarized the process for brevity.
g. If any of these engineers ceases to be part of the project, that Authority having jurisdiction (the city) must be informed immediately by the owner. Failure to do so will attract a citation which comes with a huge fine or imprisonment. Furthermore, the aspect of the job of the engineer must be stopped until a replacement is in place and the city is notified.
From your descriptions, there are different specifications for types of buildings (like commercial, residential), including where they should be sited. Why are these standards not so clear in Nigeria?
Good question. My warehouse in Owerri is in what they call an estate. At first, I did not want to site the project there because there are so many residential houses in the area. When I asked the local government, they said that I can site my project anywhere since I own the land. I was pleasantly surprised. The reason I continued with the project is because I know that the warehouse is for light industrial manufacturing that will not produce any harmful, environmentally unfriendly or noise-generating operations.
It is noteworthy to state that, even here in Canada, there are mixed-use zoning where there is a mixture of residential and light industrial and commercial. However, these are strictly regulated. My association here have been trying to buy a building to be used as a town hall where we meet and engage in our social activities. Our challenge has been that the city will not allow us to convert potential units in industrial properties to such use due to zoning restrictions. Because we want to have food preparation area (kitchen) in the property, town halls are not permitted in industrial building with other occupancies except if it is a standalone building.
Zoning is very important for the health and safety of people. You cannot build a school or hospital in the same area like a factory. Zoning is not only for residential, commercial and industrial. In each of these classifications, there are micro zoning. For instance, zone high-rise residential building will not be allowed in the same area where you have a single-family building, otherwise, it will depress the market value of the single-family homes. Similarly, light, medium and heavy industrial cannot be located in the same zoning area.
How would you rate official monitoring of building projects in Lagos and the rest of the country and what specific supervisory changes would you want to see immediately?
The current supervisory standard is pathetic and abysmal. That’s all.
What generally can you say about the disaster at Ikoyi; could it be as a result of use of quacks in executing the project, or substandard materials that did not adhere to specifications?
It will be unprofessional for me to comment or conclude on the quality of the material or workmanship without seeing test results of the components, review of the building design, contractor experience, soil test results and other relevant documents. That said, there are some tell-tale signs that can provide a window into what happened. A trained and discernible engineer can pick out some of this evidence from miles away. From video images and footage on TV and the Internet, the sizes of the rebar (iron rod) look grossly undersized for a two-storey building, how much for a 21 storey building. If the rebar is undersized, one can deduce that other components and materials used in the building are equally questionable.
One of the questions that should be asked about the design of this building is: Was a wind tunneling simulation done for the building. Ikoyi is a coastal area with a wide-open water body. Wind more than even dead and live load should govern the design of any building in that area. This is one of the reasons I said that all the required information should be available before one can make a professional judgement about the collapse.
While casting light on material and workmanship, how adequate is our National Building Code? Is it sufficient, related to our local condition (because every building is local and no two construction sites are the same), or was it a copy and paste from another country, without the same environmental similarity with Nigeria? Even in Nigeria, there are varying conditions. As such, our building code should not be a one-size-fits-all but must reflect these environmental and climatic differences
What are your general comments on the strength of materials used in building construction in Nigeria?
Materials used in construction in Nigeria are criminally substandard or have no standard at all. For instance, does the road size block maker know the compressive strength of the block required for a different type of and sections of the building? Luckily in Nigeria, most of our storey buildings do not rely on blocks as structural components or load-bearing members. The blocks are merely curtain walls that has no structural relevance except to account for its dead weight in sizing beams columns and foundation. That said, do those block makers know the required mix design and water-cement ratio to provide the expected compressive strength in the block? The answer is no.
Not because they do not want to, but because nobody taught them the relevance. Coming to site batched concrete, what is the mix design or water-cement ratio. Who designs it? Is there a test for the slump? What strength is the concrete required to achieve in 7, 14 and 28 days? What is the carbon content of the iron rods used in Nigeria? Who checks it. What is the standard and specification of the iron rod? Is there a reliable documentation that truly reflects the quality of the material? What does the building code say about it? If we leave material for a while and look at the workmanship, do our “builders” know how long the concrete should cure before a load is placed on it? How do they know if the strength has been achieved without a test? Do they know how much live load can be safely placed on the newly cured concrete? A whole lot is wrong with our system.
I was asking an architect friend if he had a copy of Nigerian National Building Code and he said no. I was shocked because this architect has been building multi-billion naira buildings in Abuja. The building code is like a Bible to anybody in the building industry. It should be part of the curricular of all building-related programmes in high institutions. I have limited my comments on structural components. But in all aspects of our buildings, there are no standards. A 1.2 m door is hardly up to 1.1 m. That’s the same story all over.
Talking about structural engineering professionals, is there a way to regulate them just to ensure that only qualified persons are allowed to practise?
I don’t think that non-structural engineers are practising like one. An engineer must stamp and sign any design he or she produces. A non-structural engineer cannot sign and stamp a drawing. If somebody is parading him/herself as a structural engineer, it is criminal and not peculiar to engineering. Every profession is beset with such challenges. The industry should be self-regulating, similar to what is obtainable here in Canada and other professions. The question is: How strong is the code of ethics of the profession and how serious is the disciplinary process. An unqualified engineer, and especially structural, is not only a danger to him/herself but also to the society.
If an Accountant makes a mistake, money is lost; if a lawyer makes a mistake; somebody goes to prison or some lives are lost; if a doctor makes a mistake, a life is lost but if an engineer makes a mistake, so many people may die. Ethics is one of the most important factors in any profession. For instance, irrespective of who is hiring me for a job, my first responsibility is towards the society or public and not to the person paying the bills. That’s the oath every engineer in Canada takes. The next responsibility is towards the client, profession and then the engineer, in that order. So, if a client asks me to use a 12 M iron rod to save money when I know the right design is to use 16 M, I’ll refuse. Not only will I refuse, I have obligation to report that incident. Failure to do so makes me culpable in case of any mishap. Similarly, if I’m hired to do a job and I encounter an unsafe situation, I’m obligated to include it in my report, even if it is not part of my scope and my client doesn’t want me to do so. Finally, on this, engineering ethics standard states that an engineer can only engage in a practice or job where the engineer is qualified by training or experience to undertake. So, as an engineer I cannot undertake to design 21-storey building if I’m not trained or experienced to undertake such design.
Follow Us